Hey guys,
The picture is of two parts produced with the SLS RP Process. You get a metal piece that has similar characteristics of 7075 aluminum. It’s the same file used (STL), and can be high temp silver soldered, big bonus!
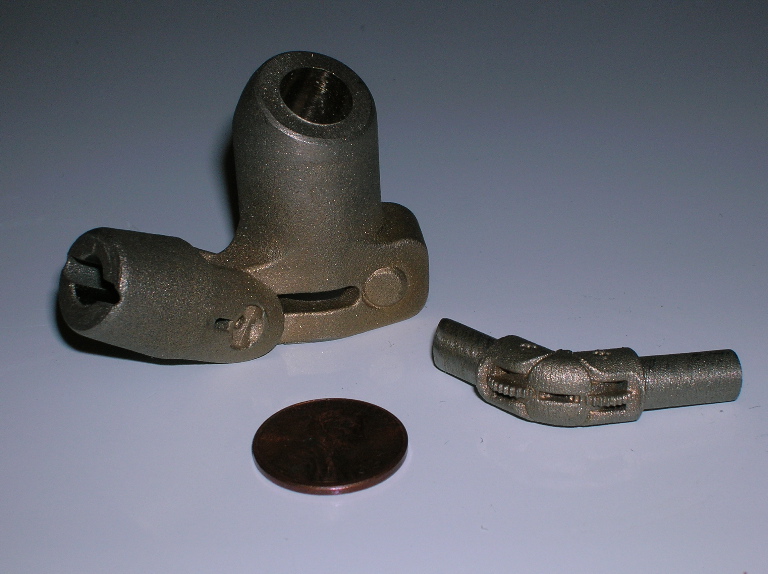
Each piece started as an assembly of individual parts in my CAD app, I had to machine these individual pieces in full scale, and create a working mechanism. The smaller of the two was 2"dia at full size.
What I did was convert the assembly into one part and scaled it down, export as STL, email off to my vendor, 30 hours later and lots of $ paid, had 36 SLS parts in hand.
Two things to look at:
For the quantity of parts it is impossibly fast compared to machining. The math comes out to 49 minutes per piece. But unfortunatly, it would be 30 hours if I ordered only one piece too. Also, I could not really get the geometry exactly like the model without some post-work.
Translation: no time to machine them.
However, The STL file was at the highest resolution. As you can see, there are lines showing the layer build-up. As I noted earlier, the parts were supposed to look like the machined (full-sized) counterpart. But given that I needed the metal part, what it looked like was more like a cast part.
From the machine this was as good as it gets.
So, hopefully this can help show how there is no one best approach. You got to try them all, then be able to decide which is best for the job at hand.