Oh no!
I’m not sure how we ended up in a worse situation than we were originally. Where did all the geometry near the center line go?
To be clear, with M&W just use it directly on your original, intact mesh. Don’t bother deleting half or trying to match up two ill-fitting halves. It isn’t necessary.
Originally you were having trouble because you were trying to weld together two pieces that didn’t quite match up at the center line. With Mirror and Weld though you’re only working with a single mesh, and it will weld the geometry at the center line as long as that half is close enough to the mirror plane. If the figure is symmetrical and mostly flush with the mirror plane at the center, that should be all that’s required.
This is why I had you switch on the mirror plane to visualize the center line. If your mesh is off center, you may have to move the target half closer to the mirror plane to get better results.
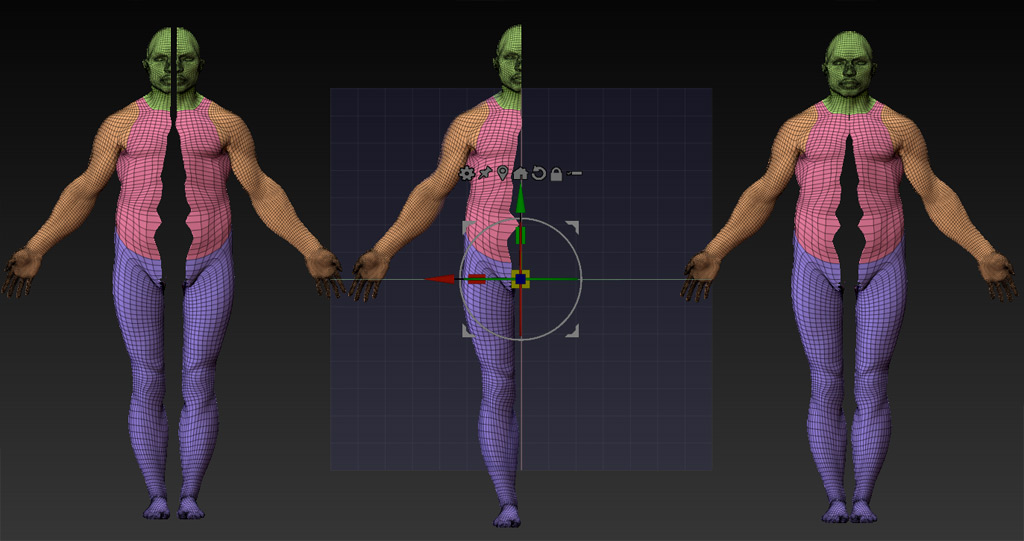
If there is geometry near the center line causing a seam issue, then simply move it across the mirror plane and perform another Mirror and Weld. The problem geometry will be cut off:
In extreme cases of an off-center mesh that is not flush with the mirror plane it may be easier to extrude some geometry from the target half first, rather than to try to bridge it after the mirror.:
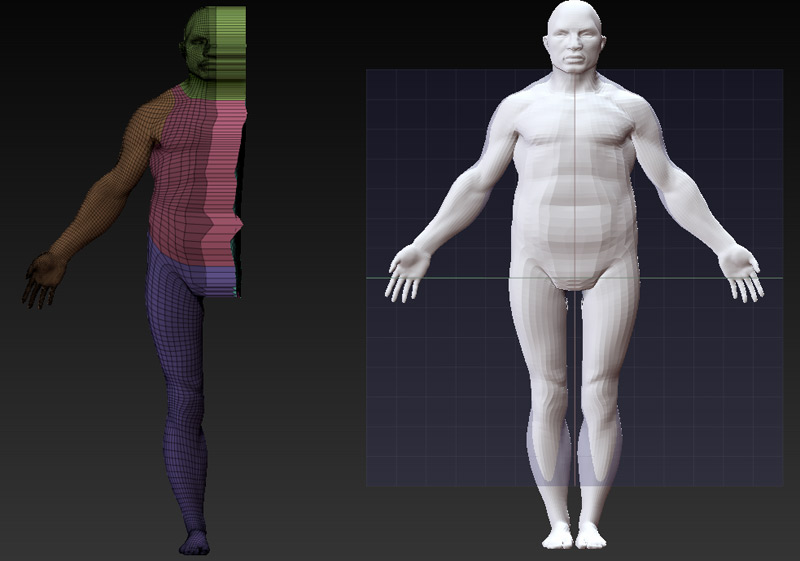
This may result in some messy topology and alter your form significantly though, so it is better to not end up in this situation in the first place with mesh discipline.