I had been inspired by a Selwy post back in '12 where he used a company in Italy called 3DWood.
In '13 I used them for a project, and I was very satisfied with the final results.
But there were some unforeseen awkward difficulties. My shipment got caught up in Customs for a month
because it had apparently come into contact with an angry bottle of olive oil.
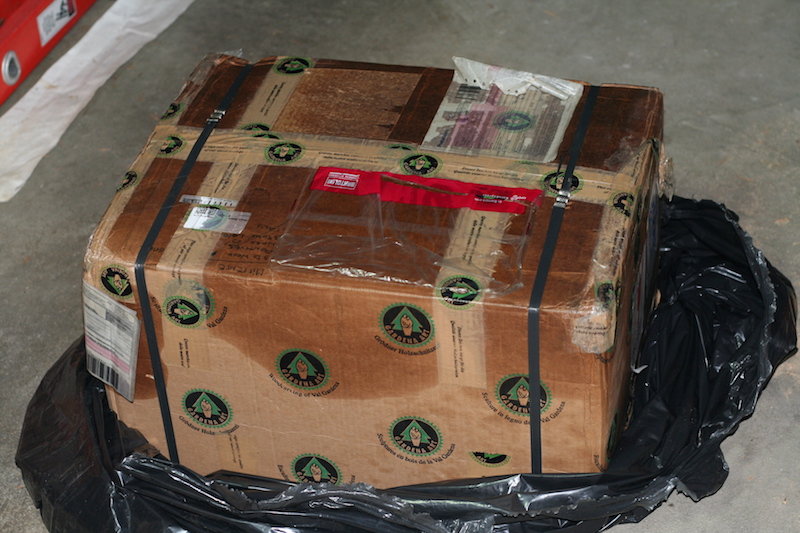
So I wanted another solution, closer to home. I had chosen 3DWood in the first place because it was so hard
to find anybody in the USA that would cnc anything beyond a sign. (2 or 3 axis cnc)
About that time PocketNC had a successful Kickstarter for a desktop 5-axis cnc. After they had shipped their
Kickstarter models, I became customer #020 for their public offerings.
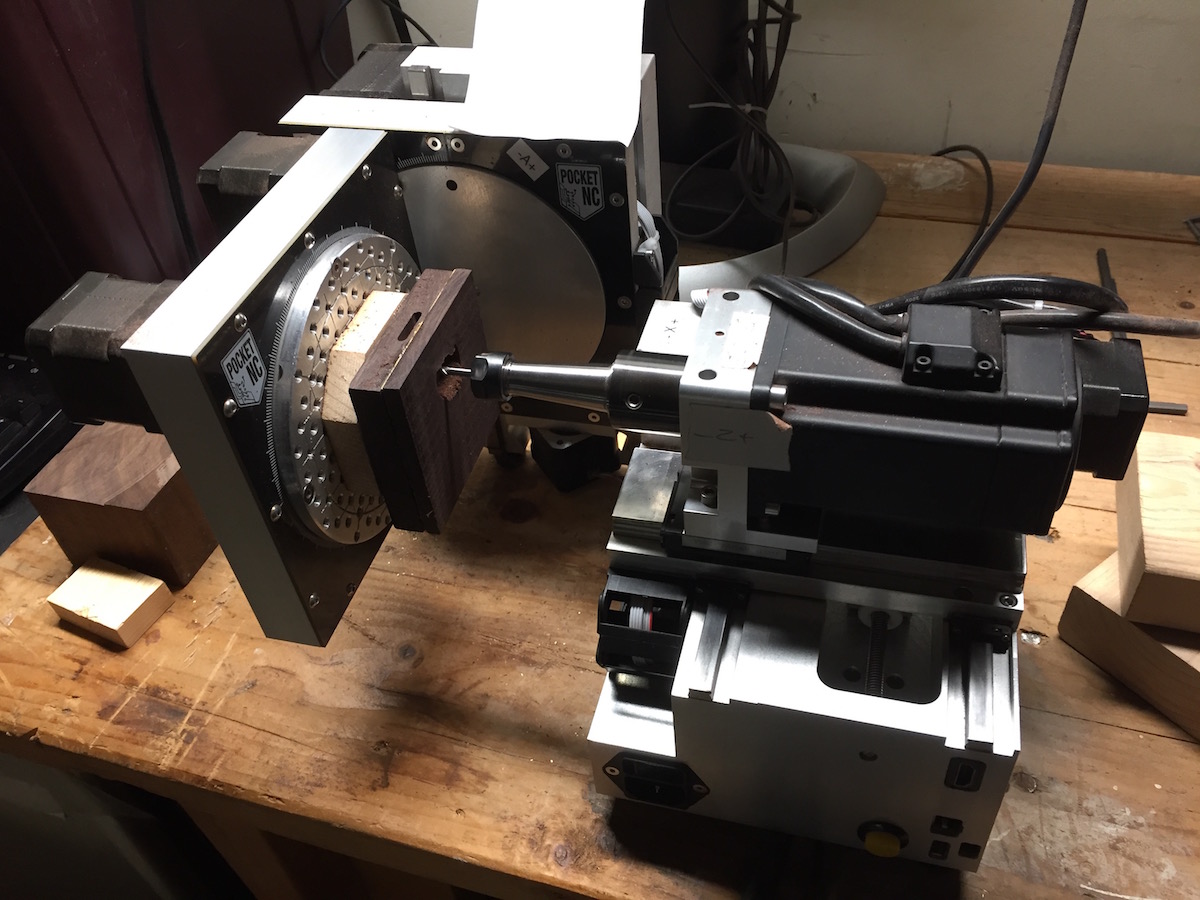
The PocketNC came with one year of Fusion360 (now its free until you make bank).
That has been the source of confusion for me over time.
Just because the PocketNC is 5-axis (but no Lathe), Fusion360 had no 5-axis features when I first got it.
Fusion360 now has Swarf and Multi-axis Contour, but they want T-Spline geometry to follow,
and that brings me to .stl and .obj files.
Originally, Fusion360 required all geometry for CNC CAM to be T-Splines, and it had a 10K face limit.
That posed a serious problem for exported ZBrush files. STL’s are chaotic, but even a structured OBJ file
would yield inconsistent results converting to T-Spline.
And then, even if you get a great T-Spline conversion, there might still be a gotchya. Here I threw at it
what I assumed was a simple small piece of geometry.
My Duael Designs Logo. As you can see in this Fusion360 simulation, there are areas under the lip that don’t get cut.
Fusion Customer Support took a look at this geometry and concluded that the code could not “see” under the lips that far.
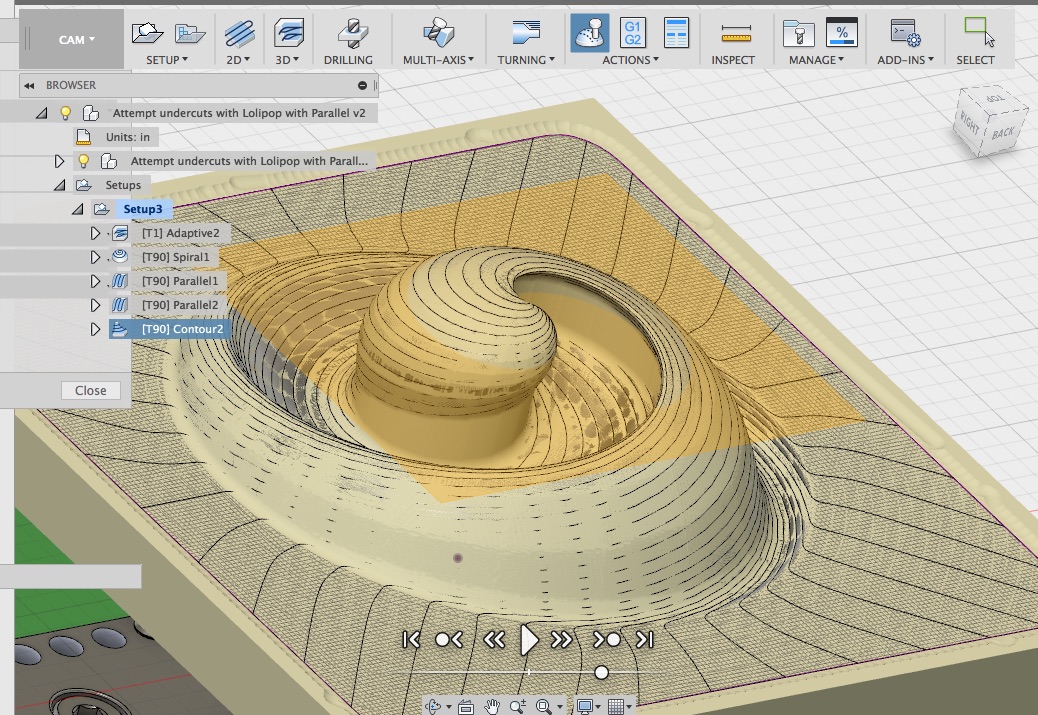
Now, as of May '17, you can bring .stl files directly into CAM in Fusion360, bypassing the need for
conversion to T-Spline, BUT, you still don’t get to use the 5-axis features because they still want
T-Spline curves to follow.
(Visualize yourself laying a pipe on train tracks and rolling it down the tracks. The pipe is your milling
drill bit and it cuts flat everything in between the tracks. That’s 5-axis Swarf. )
So, the geometry I have used here is a result of my struggle dealing with T-Spline geometry conversion
and my desire to use the 5 axis features, while continuing to work in ZBrush.
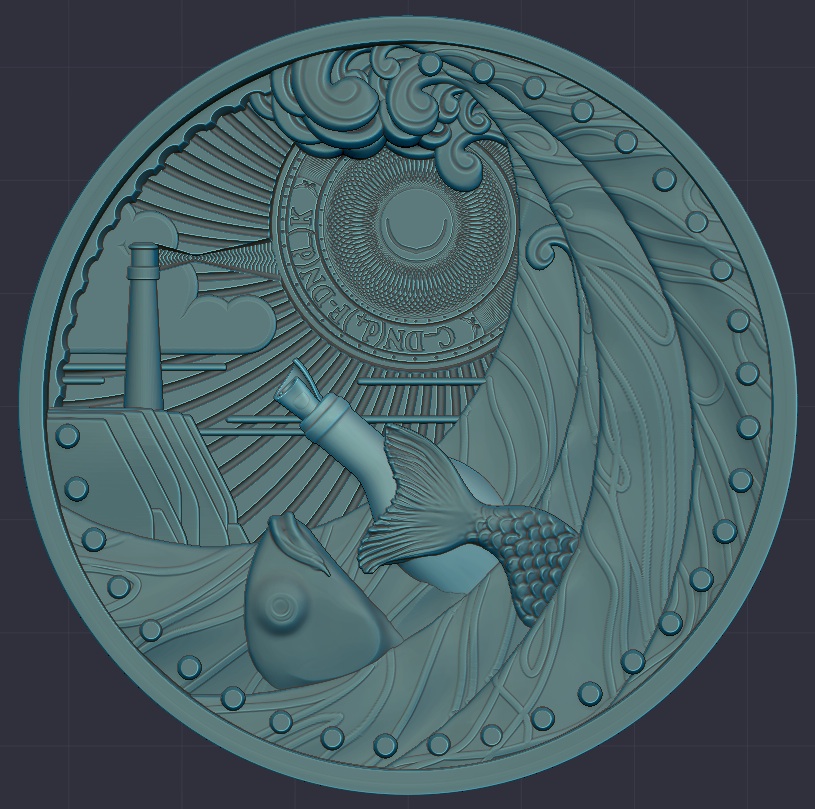
As you can see, it looks NURBS-ish, and that was my early solution to getting a T-Spline conversion
that was as useful as possible.
ie; resulting in complete curves along an edge that didn’t stop midway and go 90 degrees for no apparent reason.
It occurred to me that if Fusion360’s T-Spline conversion could recognize ZBrush Polygroups, there could be
a greater possibility of useful results, as it would be one extra layer of information.
But with the May '17 update, I decided to concentrate on my other concerns, and save the potential of T-Spline curves for later.
My goal was to cut multiple materials, Brass and hardwood, where the brass was sandwiched and would be revealed.
The reason for these materials was the Story. The Story of Dark Money, which I will get to later.
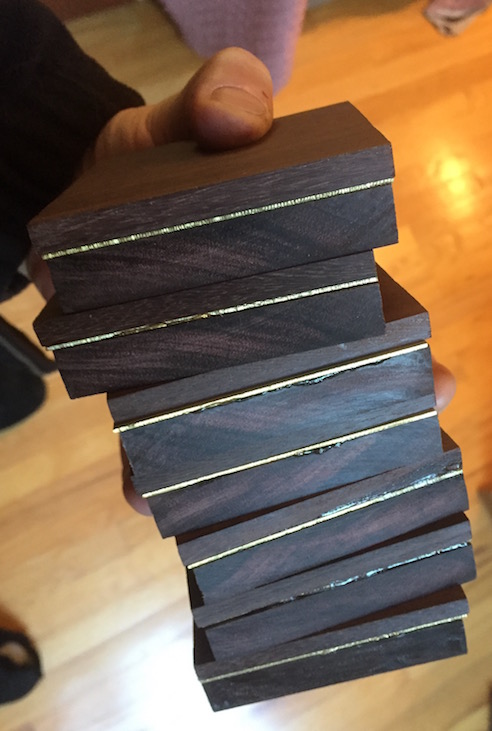
As I am not using geometry that would allow for 5-Axis milling, what I am really doing is referred to as 3+2 milling.
While there are a dozen type of milling paths, my stl geometry required a small Ball End Mill using close
parallel passes for the Finish Pass.
I started cutting Machinable Wax first, as its easy on your tools, faster to cut, and shows you your detail level.
Once I felt I had a reasonable understanding of the cutting paths and milling bits, I switched to layered woods.
I didnt want to break bits hitting the metal wrong, so I practiced on wood, using a Maple veneer in between
Black Oak, with the veneer being 0.04in.
Wood being wood, there was a 0.01 possibility of error in a stack of 3 woods laminated, then screw
attached to a 1/2 piece of pine Sacrifice stock, which is screw mounted to an aluminum mounting plate,
courtesy of Randy Kopf. The error would be worse if you don’t pay serious attention to clamping.
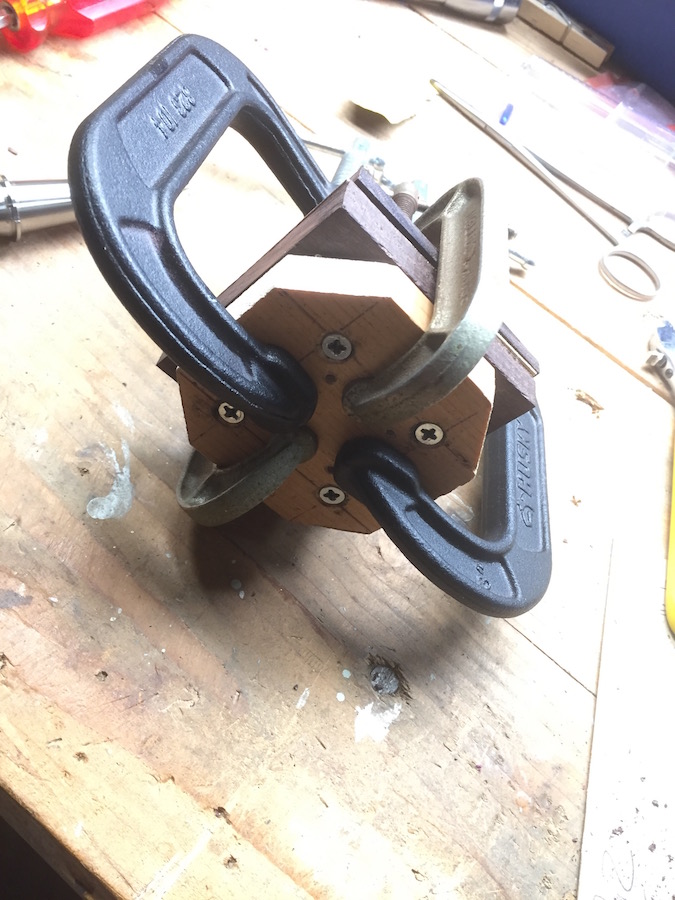
I needed to make sure I could kiss the face of the brass with a Flat End Mill to get a polished surface,
and not go to deep thereby leaving enough metal for the engraving bit to not pass through the other side.
The veneer is 0.04, but the Brass will be 0.06, with the engraving bit being a Harvey #989725, which
has a 0.025 diameter tip.
This bit is a Harvey #989715, with a ball tip diameter of 0.015, of which I broke two trying for the
ultimate in detail level, as this is the smallest bit I can find on planet Terra.
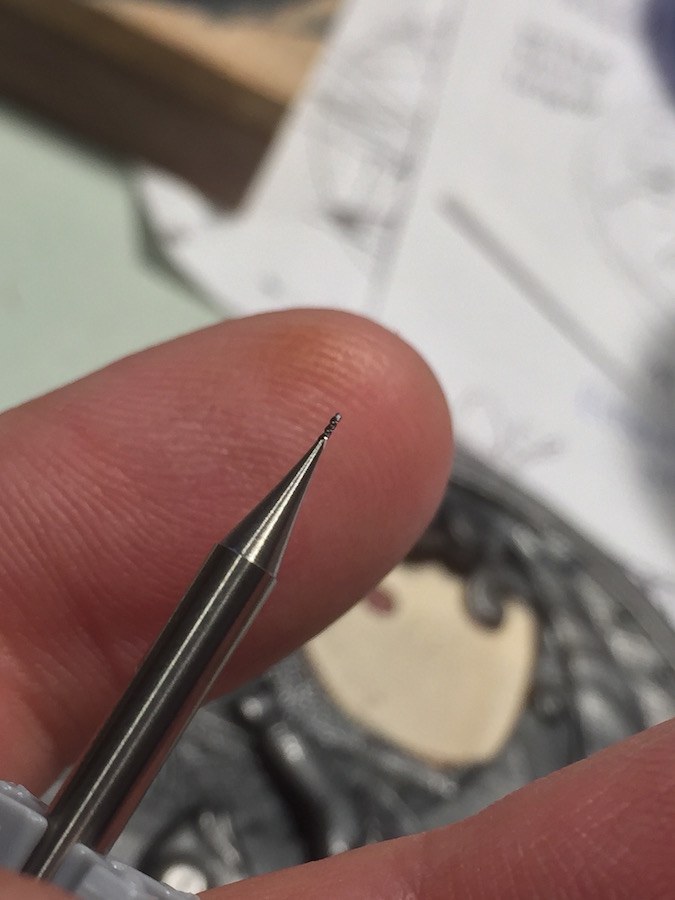
Gotta go for now. End of Part 1
~ more to follow ~